Selection of impact modifiers for polymers
Expand articleImpact modifiers are added to plastic blends to improve the durability and toughness of various plastic resins. Depending on the end application and the internal resistance of the polymer, formulators must achieve very different levels of impact resistance, from general purpose to ultra-durable.
What are impact modifiers for?
General purpose impact modification
General purpose impact modification is a very low level of impact modification that is used, for example, to avoid conditioning of molded polyamide parts.
- This means acceptable impact toughness at room temperature, but does not take into account any requirement for low temperature (below 0°C) impact toughness.
- Most applications of this type require only low levels of impact modifier (<10%), and the impact modifier need not contain reactive groups to be acceptable for the application.
Low temperature impact modification
Low-temperature impact toughness is essential for applications that require a certain level of low-temperature flexibility and fracture resistance. This is, for example, the case for many applications in the field of household appliances. This requires modifiers containing 5-15% predominantly reactive modifiers.
Ultra-high strength
Ultra-high impact toughness is required for applications that should not result in part failure even when impacted at low temperatures (-30 to -40°C) at high speed. This requirement can only be met with a high content (20-25%) of a reactive impact modifier with low Tg.
In addition to impact toughness, impact modifiers can also help improve other material characteristics such as:
- Optical and tensile properties
- Weather resistance
- Processability
- Flammability
- Heat distortion
How do impact modifiers work?
The elastomeric and rubbery nature of impact modifiers absorbs or dissipates impact energy. Impact modifiers can be incorporated by polymerization in a reactor or can also be incorporated as additives during the compounding step. Two mechanisms by which impact modifiers work are discussed below.
Craze Propagation
The principle is to disperse impact modifiers in a brittle matrix, a damping phase capable of absorbing energy and stopping crack propagation.
Shear Band/Cavitation
The second mechanism is the formation of shear bands around the elastomeric particle, which absorb the deformation energy. This mechanism is always accompanied by cavitation of the damping particle (appearance of voids), which also absorbs energy. However, the appearance of shear bands absorbs most of the energy.
To be effective, the dispersed phase must have the following properties:
- Dampening capability: The elastomeric phase is recommended. Generally, low glass transition materials and low crystallinity polymers are used. Low Tg is absolutely required for low-temperature toughening. Polyolefin copolymers are excellent candidates.
- Good cohesion with the continuous phase: this parameter is key for effective hardening. Lack of cohesion can initiate multiple cracks which can then propagate to fracture. Good cohesion can be achieved by specific interactions at the surface or by reactivity. Combination occurs through the formation of "amphiphilic" copolymers at the interface, reducing surface tension and increasing adhesion.
Polymer compatibility also affects the size, regularity and stability of the dispersion, which positively affects the mechanical performance of the finished part.
Functionalized polyolefin impact modifiers
In order to fulfill the industry requirements, polymers, such as polyamide, polyester, PVC or bioplastics, need improved impact resistance.
Among the impact modification technologies available on the market, polymer impact modifiers, also known as functionalized polyolefins, offer a full range of strengthening characteristics from general purpose to super-hardening in a variety of polymer systems.
Polyamides (PA)
A wide range of impact modifiers based on functionalized or non-functionalized copolymers or ethylene ionomers can meet the unique needs of your PA 6, PA 6,6 or fiberglass reinforced PA compounds.
Industry-leading impact resistance:
- Super-tough impact resistance
- Low-temperature toughness
- Intermediate toughness at reduced cost
Additional benefits:
- Improved flow for better performance
- Aesthetic properties (class A, excellent surface finish, excellent coloration)
- FDA compliance for direct contact with food products
Polyesters (PBT, PET)
Polymer impact modifiers for engineering polymers or cast sheets offer a wide range of performance levels, allowing you to create customized solutions that meet your unique needs.
- Engineering polymers: For the most demanding applications, some polymer impact modifiers provide ultra-high impact toughness in virgin and glass fiber reinforced compounds. However, when compounding PBT engineering polymers, the challenge is to improve impact toughness while maintaining the original properties.
Among a wide range of offerings, these impact modification solutions provide compounders with a valuable new tool for tailoring the properties of PBT resins to meet the requirements of electrical and electronic connectors, as well as a wide range of other industrial and consumer products. - Cast sheet applications: Improving performance while achieving the required impact toughness properties is a very challenging task when it comes to PETF-based cast sheet applications.
Advantages in the application of engineering polymers | Advantages in the application of cast sheet |
|
|
---|
Polyvinyl chloride (PVC)
Depending on the end use, different types of PVC resins need different impact modification additives to achieve the desired performance characteristics.
Flexible PVC | Rigid PVC |
|
|
---|
Polypropylene (PP)
Polypropylene is a semi-crystalline polymer that has a very attractive price/performance ratio and is easy to process. However, to meet some industrial needs, polypropylene requires increased impact resistance at ambient or low temperatures.
Impact modifiers improve the strength of polypropylene at room or low temperatures. The wide range of products allows us to offer a unique and customized solution for each situation.
Additional benefits:
- Improved dispersion of pigments, glass fibers or mineral fillers
- Improved compatibility for polypropylene alloys
Acrylonitrile butadiene styrene (ABS)
ABS resins are on a level between engineering plastics such as polycarbonate and commodity materials such as polystyrene. They are widely used in applications such as computer and printer housings, consumer electronics, appliances, gardening equipment, automotive parts and toys.
While producing ABS compounds, whether standard, recycled or filled, poor toughness can be encountered.
Impact modification is a very complex problem for which there is one specific solution depending on the temperature required to achieve the overall strength characteristics.
Additional benefits:
- High compatibility
- High dispersibility (allows for changes during processing)
Polycarbonate compounds (PC/ABS, PC/PBT)
Modern requirements for polycarbonates are related to high impact toughness at low temperatures while maintaining good processability, which makes it possible to efficiently produce highly specific parts and profiles, e.g. for the automotive industry, by injection molding.
Depending on the polymer used to mix the PC-based resin and the desired viscosity level, a specific additive is required.
Compared to alternative technologies, additional advantages can be found in the following:
- Better compound recyclability due to lower melt viscosity
- Better UV resistance and heat resistance
- Higher elongation
- Easier transportation and recycling due to granule form rather than powder form
Core-shell impact modifiers
These materials typically have a low-TG rubber core, such as butyl acrylate or butadiene, with a sheath of poly (methyl methacrylate) PMMA.
One of the main advantages of the core-shell impact modifier method is that a predetermined particle size is provided. However, for the impact modifier to be effective for strengthening engineering plastics, it must be properly dispersed in and bonded to the matrix polymer.
This bonding can be the result of physical interaction of the sheath matrix with the matrix or a chemical reaction. The most obvious way to do this is to combine reactive fragments in the sheath chain during fabrication by emulsion polymerization. These reactive fragments subsequently react with the matrix during melt processing.
MBS impact modifiers compared to acrylic impact modifiers
Butadiene-styrene methacrylate (MBS) | Acrylic exposure modifiers |
Advantages:
|
Advantages:
|
---|---|
Application:
|
Application:
|
- MBS core-shell impact modifiers are designed to provide exceptional low temperature impact in a wide range of engineering plastics such as polycarbonate, polycarbonate alloys (PC/ABS, PC/PBT) and polyesters.
- The core-shell impact modifier gives polycarbonate better low-temperature impact strength, color castability and thermal stability than any other acrylic available on the market.
MBS impact modifiers in polycarbonate
Polycarbonate (PC) is known for its transparency, superior impact resistance and ability to withstand high temperatures throughout the life of the final product.
However, the low chemical resistance of PC (to gasoline) is a problem for automotive applications. Another limitation is the injection molding of highly viscous grades, especially when high impact resistance is required.
In addition, the inherent characteristics of PC, such as impact resistance, are also seriously degraded when colored pigments, fillers, or flame retardants are used in the mix.
Recycled PC is a cost-effective solution for compounders. However, the recycling steps reduce the mechanical characteristics of PC, making it necessary to use impact modifiers in recycled PC to achieve the desired performance level.
Benefits of MBS impact modifiers in polycarbonate:
Advantages | Description |
Exceptional low-temperature impact characteristics |
|
---|---|
Excellent resistance to weathering and heat aging |
|
Exceptional dyeing ability in injection molding applications |
|
MBS impact modifiers in polycarbonate compounds (PC/ABS, PC/PBT) (PC/ABS, PC/PBT)
To meet new market demands, including technical performance but also cost, compounders have developed polymer blends that balance the superior benefits of polycarbonate with the unique value for money characteristics of other matrices such as ABS or polyesters (PBT).
These polymer blends provide high performance compared to traditional PC. These blends help:
- Overcoming poor flow and brittleness characteristics - A rubber phase, such as acrylonitrile-butadiene-styrene (ABS), can be added to the PC matrix to improve the flow characteristics in opaque applications of high-strength PC.
PC/ABS is today's fastest growing PC grade where ABS allows a balance of high impact toughness, surface finish and high flowability for better processing. The disadvantage is that PC/ABS mixtures often do not meet the new flame retardancy standards.
The most common end users of PC/ABS are automotive parts, office equipment enclosures, computers and cell phones. - Overcoming low chemical resistance - Polycarbonate is known to have very low chemical resistance, which is a critical characteristic in the automotive industry when in contact with oil and gasoline.
To overcome this weakness, polycarbonate and polyesters such as PBT are blended to produce an alloy with high chemical resistance, which unfortunately results in poor impact performance of PBT.
But when it comes to processing, adding fillers, color pigments or flame retardants, all of these mixtures lose their original critical strength values.
Benefits of MBS impact modifiers in polycarbonate compounds:
Advantages | Description |
Better compatibility | The high impact toughness of PC/ABS alloys will largely depend on the ability to well disperse the various polymer phases (PC, PB, SAN), which is usually achieved with technical compounds. |
---|---|
Excellent low-temperature effect | Their low glass transition temperature (Tg<-80°C) on impact allows them to be used for demanding low temperature applications to create products that can withstand temperatures as low as -50°C and maintain their structural integrity. |
Good dispersibility | Impact modifiers are easily dispersed using conventional compounding methods. The resulting engineering plastics blends are easily poured into molding equipment and have exceptional impact toughness resistance. |
MBS impact modifiers in polyesters
Polyesters such as polybutylene terephthalate (PBT) and polyethylene terephthalate (PET) are semi-crystalline polymers showing very attractive characteristics such as high temperature resistance and chemical resistance. On the other hand, polyesters show low resistance to low temperature impact, so impact modifiers are needed.
Polyesters are often used in automotive applications, such as power window actuator housings and light-conducting housings. They are also used for many household appliances, electrical engineering and medicine.
Advantages of MBS impact modifiers in polyesters:
Advantages | Description |
Excellent low-temperature effect | The low glass transition temperature (Tg<-80°C) of impact modifiers allows them to be used for demanding low-temperature applications to create products that can withstand temperatures as low as -50°C while remaining ductile. |
---|---|
Good dispersibility | Impact modifiers are easily dispersed using conventional compounding methods. The resulting engineering plastics blends are easily poured into molding equipment and have exceptional impact toughness resistance. |
Thermoplastic elastomers (TPE) as impact modifiers
A thermoplastic elastomer is generally defined as a polymer that can be processed as a thermoplastic material, but also has the properties of a conventional thermosetting rubber.
Some of the common classes of commercial TPEs include:
- Styrene block copolymers
- Thermoplastic polyurethanes
- Thermoplastic copolymers
- Thermoplastic polyamides
To be classified as a thermoplastic elastomer, the material must have the characteristics listed below.
- Ability to stretch to moderate elongations and return to a shape close to the original shape after stress is released
- Recyclability as a melt at elevated temperatures
- No significant creep
TPE – Advantages and disadvantages:
Advantages | Disadvantages |
|
|
---|
TPEs are often used when conventional elastomeric materials cannot provide the range of physical properties required for a product. Thus, their use depends on the end use, and specific TPEs are used depending on the end need.
This is another example of the requirement to achieve an appropriate balance of elastic modulus and impact properties during impact modification of engineering plastics. This feature is relevant and important for all described approaches.
Bulk elastomeric compounds as impact modifiers
The approach to using bulk elastomeric compounds as impact modifiers differs from the use of core-shell type materials, as the size of the dispersed rubber phase depends on the processing conditions used. This allows the particle size in the final impact modified product to be controlled.
Disadvantages of using elastomers as impact modifiers
One of the biggest drawbacks of this approach is that the stiffness reduction seen with the addition of elastomer is typically greater than with core-shell type modifiers. This means that if maintaining the stiffness that the engineering plastic provides is critical to the application, the elastomer concentration must be adjusted accordingly. An example is the modification of PBT using an elastomeric blend.
In this case, the processing conditions of the PBT/elastomer blends affect the particle size of the elastomer and thus the impact modification achieved. In addition, the relative viscosity of the components affects the morphology of the final blend. Since melt viscosity is directly related to the molecular weight of the polymers, it follows that molecular weight is an important factor in determining the observed impact modifications.
Based on SpecialChem
■
Nylon 66 fibers: properties, application, advantages.
Expand articleThere are several polyamides that have been developed as fibers. The common name for these products is "nylon. Nylon is defined as a general term for any long-chain synthetic polymer amide that can be formed into a filament in which the structural elements are oriented in the direction of the axis.

Nylon was the first of the "miracle" filaments made entirely from chemical ingredients in a polymerization process. Polymer crumb nylon 66 can be extruded into filaments or formed into a variety of prefabricated engineering structures. The fibers are drawn, or stretched, in a process that increases their length and reorients the material molecules parallel to each other to produce a strong, flexible filament. Nylon's thermoplasticity allows for continuous crimping or texturing of the fibers and provides volumizing and stretching properties.
The advantage of nylon fiber design
In 1939 the appearance of nylon in sheer stockings revolutionized the market for women's hosiery. Silk and cotton were quickly superseded by this more durable and easy-care material. Nylon soon found its application in other areas as well. In parachutes and fishing lines, nylon became a moisture- and mold-resistant substitute for silk. In body armor, nylon provided previously unattainable strength and durability for protection against projectile fragments. And when nylon was used to reinforce aircraft tires, it allowed heavy bombers to land safely on makeshift runways. Today, manufacturers offer a wide range of Nylon-66 polymers for use in industrial, textile, furniture and flooring applications.
Advantages of Nylon 66
Nylon 66 is a semi-crystalline, off-white engineering thermoplastic that is the strongest and most abrasion-resistant unreinforced aliphatic nylon with better low-temperature toughness than Nylon 6 or acetal. Nylon 66 outperforms Nylon 6 in many applications due to its outstanding dimensional stability, higher melting point and more compact molecular structure. For example, Nylon 66 gives only half the shrinkage of Nylon 6 when exposed to steam. And, with a less open structure, fiber 66 has good resistance to dye washout, resistance to UV radiation and excellent performance in high speed spinning processes. Typical advantages of nylon 66 over nylon 6 are:
- Higher tensile strength
- Excellent abrasion resistance
- Higher melting temperature
Nylon 66 provides high tensile strength for:
- Excellent performance for tire applications
- High-speed milling
Excellent abrasion resistance makes Nylon 66 polymer ideal for manufacturing:
- Carpets
- Stuffing
- Conveyor belts
The rubber industry takes advantage of Nylon 66's high melting point for high-temperature curing of tires. The high melting temperature also causes the fiber to have:
- High stretchability and recoverability in textured yarns with false twist (e.g., hosiery)
- Thermal stability during high-temperature coating application
Using Nylon 66 in fiber production
Nylon processing usually starts with conditioning the resulting crumb, with or without increasing the resulting molecular weight. The chips are then melted, usually in a screw extruder, and extracted as filaments. The filaments are then packaged in a process that may include pulling, compacting, or cutting into staple pieces.
Fibre properties Nylon 66
Physical properties
Like nylon 6, different types of nylon 66 fibers have different physical properties.
Property | Staple fiber | Regular thread | High-strength thread |
Density (g/cm3) | 1.13 | 1.14 | 1.15 |
---|---|---|---|
Moisture (%) at: 65% RH 100% RH | 4.0-4.5 6.0-8.0 | 4.0-4.5 6.0-8.0 | 4.0-4.5 6.0-8.0 |
Tenacity (g/d) dry wet | 3.0-6.8 2.5-6.1 | 2.3-6.0 2.0-5.5 | 6.0-10.0 5.1-8.0 |
Elongation (%) | 16-75 | 25-65 | 15-28 |
Stiffness (g/d) | 10-45 | 5-24 | 21-58 |
Thermal properties
Due to the different structure, the melting point will be in the range of 249°C to 260°C. The glass transition temperature of this fiber ranges from 29°C to 42°C. The softening temperature, ie the sticking point, is 230°C. The fiber becomes discolored if kept at 150°C for 5 hours. The thermal deflection temperature is 70°C. The decomposition of this fiber starts at 350°C.
Chemical properties
Nylon 66 fibers are more resistant to acids or alkalis than Nylon 6 fibers due to the light intermolecular forces present in the structure. The fiber is unaffected by most mineral acids except hot mineral acids. The fiber dissolves with partial decomposition in concentrated solutions of hydrochloric, sulfuric and nitric acids. The fiber is soluble in formic acid. Similarly, the fiber is exposed to strong alkalis in extreme conditions, otherwise it is inert to alkalis. Fiber can be bleached with most bleaching agents. For the most part, the fiber is insoluble in all organic solvents except some phenolic compounds.
The fiber has excellent resistance to biological attacks. Prolonged exposure to sunlight causes fiber degradation and loss of strength.
Fibers can be dyed with almost all types of dyes: direct, acid, metal complex, chromium, reactive, disperse and pigments. However, only acidic and metal complex dyes are preferred because they have a higher stability.
Typical physical and chemical properties of nylon 66
Property | Value | Method/Standard |
Specific weight, kg/m3 | 1.14 | ASTM D792 |
---|---|---|
Density, kg/m3 | 1140 | ISO R1183 |
Melt density, kg/m3 | 965 | |
Bulk density, kg/m3 | ≈ 670 | |
Water absorption (24h), % | 1.3 | ISO 62 |
1.2 | ASTM D570 | |
Melting point, °С | 260 | ISO 1218 or ASTM D789 |
Glass transition temperature, °С | 100 | ISO 75 or ASTM D648 |
90 | ||
Self-ignition temperature, °С | > 420 | ASTM D1929 |
Flash ignition point, °С | > 400 | ASTM D1929 |
Specific heat capacity, J/g·К | 1.7 | Own method |
Thermal conductivity, W/m·К | 0.3 | Conco-Fisher apparatus |
Flammability (UL) | V2 | UL94 at 1.6 mm |
Dielectric constant | 3.9 at 50Hz | IEC 250 or ASTM D150 |
3.7 at 1kHz | ||
Volume resistivity, Ω | 1013 | IEC 93 or ASTM D257 |
Types of nylon 66 materials
- Nylon 66/6
- Nylon 66/6, 10% Fiberglass-reinforced
- Nylon 66/6, 20% Fiberglass-reinforced
- Nylon 66/6, 30% Fiberglass-reinforced
- Nylon 66/6, 40% Fiberglass-reinforced
- Nylon 66/6, Mineral Reinforced
- Nylon 66/6, 60% Fiberglass-reinforced
- Nylon 66/Nylon 6 Blend, Glass Fiber Filled
- Nylon 66, Unreinforced
- Nylon 66, Impact Grade
- Nylon 66, Unreinforced, Flame Retardant
- Nylon 66, Heat Stabilized
- Nylon 66, Extruded
- Nylon 66, Film
- Nylon 66, Nucleated
- Nylon 66, PTFE Filled
- Nylon 66, MoS2 Filled
- Nylon 66, Glass Bead Filled
- Nylon 66, 30% glass filled, extruded
- Nylon 66, Mineral Filled, NCG Fiber Filled
Advantages of Nylon 66 in specific fiber applications
When processed into fiber form, nylon 66 polymer offers many advantages for customer applications.
Hosiery
- Excellent high-speed processing
- High stretch and recovery
- High durability and strength
Weaving and Warp Knitting
- High fiber modulus
- minimizes yarn distortion possible during winding, warping, knitting, and weaving processes,
- minimizes barré and streaks during dyeing
- Wide operating window for heat setting, dyeing, and processing, this is especially important for fabric combinations with spandex
- Very good resistance to photo degradation
- Good dye light-fastness and wet-fastness
Tires and Conveyor Belts
Nylon 66 reinforced polymer heavy-duty tires and belts are capable of withstanding high temperatures and rapid curing cycles. Excellent performance is due to the high strength and modulus of elasticity of Nylon 66. Woven and modified Nylon 66 tire cords provide aircraft and off-road tires with long life and high resistance to fatigue. Nylon 66 has particular advantages in industrial products due to these properties of polyamide:
- High melting point
- Superior dimensional stability
- Reduced moisture sensitivity
Coated Fabrics
Nylon 66 fabrics withstand coating temperatures with PU, PVC, and rubber up to 200°C and display good dimensional stability for coating integrity.
Carpeting
During the late 1950s, two new developments opened up a new era for the carpet industry. First, equipment was developed to tuft carpet yarn into a backing material to produce pile carpeting. At the same time, DuPont invented a technique to impart bulk or “loft” to nylon by a fluid-texturing process called Bulk Continuous Filament (BCF). The combination of nylon 66 yarns, textured by the BCF process, yields carpets with:
- High abrasion resistance
- High resistance to pile crushing and Matting
- Ease of level dyeing
- High dye light-fastness
- High dye wet/wash-fastness
Carpets of nylon now account for nearly 70% in a market that was once the exclusive domain of wool yarns.
Furnishings / Floor Coverings
Nylon 66 offers the furnishings/floor coverings industry:
- A complete line of luster (from 0.0 to 1.0% TiO2)
- Products for direct use and post-polymerization Feed
- Products intended for color addition during remelt
- A full line of dye variant polymers for yarn styling formulations
Other uses
The application of nylon can be summarized as follows:
- Textiles: Apparel, tooth brushes, Tyre cord
- Automotive: Bearings, slides, door handles, door, airbag & window stops
- Furniture: Locks, hangers, chairs etc.
- Packaging: Film sheet
- Mech. Engg.: Drive gears, bearings, fish plates for railways lines tubing
* * *
Affordable heavy-duty grades, impact toughness and low notch sensitivity make Nylon 66 one of the best of all engineering thermoplastics.
Applications include mainly engineering components. It is widely used as a monofilament as well as a fiber characterized by its elasticity and high resistance to abrasion, for the production of clothing, carpets and industrial products.
■
The thermal break is a modern energy-efficient solution for facade structures.
Expand articleMost of the heat is lost through the zones of the external structures of buildings: windows, doors, facades. The lower the efficiency of thermal insulation, the higher the loss due to thermal conductivity, convection and thermal radiation.
In particular, windows made of an aluminum profile with high thermal conductivity are especially susceptible to heat loss – up to 40% of all heat losses in a building. I's necessary to isolate the window frames and to achieve thermal separation of their inner and outer shells to reduce the thermal conductivity of window structures. Plastic insulating jumpers – thermal breaks – are the best solution to this problem.
Insulating jumpers are characterized by very low thermal conductivity, which provides excellent thermal insulation of the window frame and the glass packet, helping to save energy and reduce heating and air conditioning costs. Thanks to thermal breaks, there is no cold in the window area, condensation, the formation of mold are prevented, the indoor climate improves and the temperature is distributed optimally.
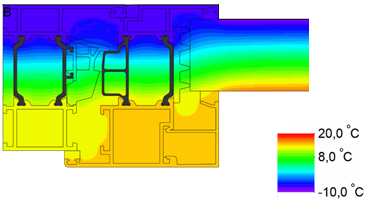
Temperature distribution inside a window structure with thermal breaks.
Recently, polyamide, in particular polyamide 6.6 reinforced with fiberglass – PA66 + 30% FG, is increasingly being used as an effective material used for the manufacture of thermal breaks.
Distinctive features of PA66 + 30% FG:
- Heat resistance.
Polyamides with excellent heat resistance can be used in the most difficult conditions, for example, in conditions of high temperature and humidity. PA profiles can significantly reduce thermal bonding, which isolates the energy flow from the outside of the facade to the inside. - High mechanical stability.
Polyamides have significant hardness and high mechanical stability for long-term use. Fiberglass reinforced polyamide is ideal for the production of structural and reinforcing profiles and is one of the best solutions for aluminum systems. Polyamide profiles protect the fragile edges of glass panels and at the same time hold gaskets to ensure air and water resistance of the structure. - Additional soundproofing.
Polyamide inserts also reduce the noise transmitted to the building from the outside, thanks to the gap they create inside the structure. - Ease and accuracy of processing.
Simple processing of polyamides is another key advantage and an ideal choice of this material for the manufacture of special extrusion profiles. - Availability and recyclability.
Thus, insulating parts made from PA66 + 30% FG are an ideal alternative to traditional aluminum glass edge profiles.
■
Glassfilled polyamides PA6 and PA66, as an alternative to metal and wooden parts of small arms.
Expand articleEngineering plastics used for the manufacture of accessories, stores, receiver elements and some other parts of small arms are used to: reduce the weight of this weapon (while not inferior in mechanical properties to aluminum alloys), attach additional accessories, and also to reduce its cost.
This article will discuss the use of composites based on polyamides of groups PA6 and PA66 glassfilled in the composition range (15-30-50)% fiberglass, with increased resistance to burning (class V-0 according to UL94).
DLG Tactical, having highly qualified designers and using fully integrated production, has developed and launched a series of manufacturing auxiliary parts and accessories for small arms. These developments, thanks to their original solutions, contribute to a more ergonomic use of various types of small arms, providing the possibility of individual use of accessories.
Consider several of the company's developments on the example of the classic AK-47.
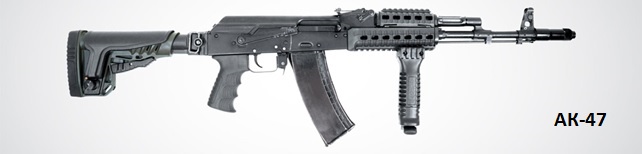
Butt
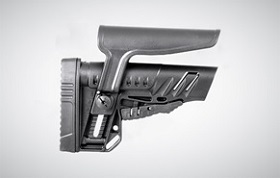
A feature of this development is the regulation of the stock in length and height, which contributes to the convenient retention of weapons during firing.
![]() | A feature of this development is the regulation of the stock in length and height, which contributes to the convenient retention of weapons during firing. |
Pistol grip
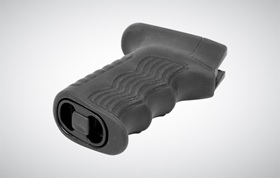
The rubberized ergonomic handle conveniently rests in the hand of the shooter, without causing uncomfortable sensations.
![]() | The rubberized ergonomic handle conveniently rests in the hand of the shooter, without causing uncomfortable sensations. |
Polymer M-LOK linings
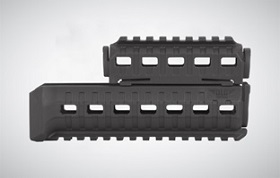
Polyamide pads with Picatinny rails serve to ensure the unification of the mounts of optical and collimator sights, as well as other accessories, including tactical lights, laser target indicators, bipods, etc.
![]() | Polyamide pads with Picatinny rails serve to ensure the unification of the mounts of optical and collimator sights, as well as other accessories, including tactical lights, laser target indicators, bipods, etc. |
Vertical handles
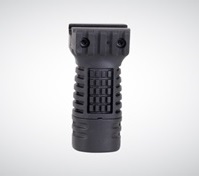
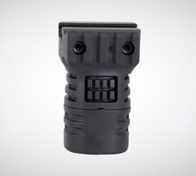
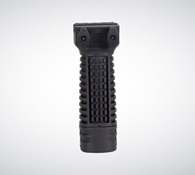
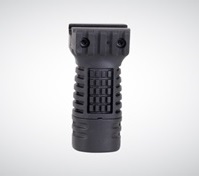
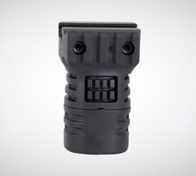
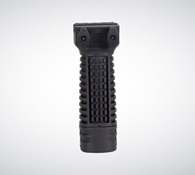
Quick-detachable ultra-light ergonomic vertical handles provide improved tactical positioning while adding a minimum of weight for small arms.
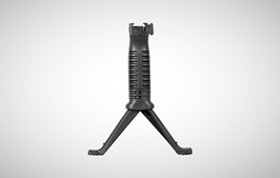
The vertical handle with a retractable stop is designed for the convenience of firing both from the “standing”, “from the knee” and “lying” positions.
![]() | The vertical handle with a retractable stop is designed for the convenience of firing both from the “standing”, “from the knee” and “lying” positions. |
For more information on DLG Tactical's product portfolio, go to manufacturer website.
■
Current Trends in Engineering Plastics Consumption in the Automotive Industry.
Expand articleThe automotive industry is the third most important consuming sector of polymers after packaging and building & construction. Therefore, changes in the material usage can have major implications on polymer demand and the financial performance of polymer producers. In this article, we provide shortly the text of article wrote by Ms. Priyanka Khemka from NEXANT.
Currently, there are about 30,000 parts in a vehicle, out of which 1/3 are made of plastic. In total, about 39 different types of basic plastics and polymers are used to make an automobile. More than 70% of the plastic used in automobiles comes from four polymers: polypropylene, polyurethane, polyamides and PVC.
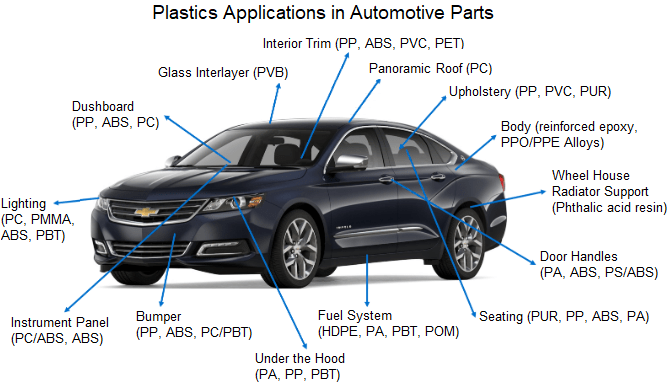
The emergence and rapid growth of electrically-powered road vehicles have become a key issue for consideration when assessing the automotive outlook and for resulting polymer demand.
Despite the growth trend for electric vehicles, automobiles that are powered by Internal Combustion Engines (ICE) will remain a significant proportion of the vehicle fleet, with polymer innovation driven by increasing fuel efficiency.
The EV vehicle design is not radically different from a traditional ICE vehicle, with the main difference being in the design and use of materials under the hood. However, electric vehicles will not have fuel system, pump, tanks, connecting cables, etc. As the market penetration of electric vehicles increases, polycarbonate (PC) consumption is expected to grow at a faster rate, as PC will be used in sensors and in LEDs in the car. The application of polymer components within engine transmission will become more common as manufacturers seek to squeeze costs and weight.
Changes in Polymer Demand PatternsThe increase in consumption of plastics such as polypropylene (PP) and polyurethane (PU) in recent years has partially been offset by the decline in consumption of engineering plastics, with PP and PU accounting for about 50% of total plastic consumption in vehicles. The consumption of engineering plastics is expected to decline due to lesser requirement of these plastics in under-the-hood applications for electric vehicles, as the high temperature resistance of engineering polymers is not required to the same extent as with internal combustion engines. Instead, polyamides will be used for battery brackets and housings in the EVs.
Polypropylene demand will continue to grow as it finds new applications in car interior and exterior, and under the hood replacing some metal parts. In addition, growth will also be spurred by increased production of EVs, which will require lighter parts to help offset the weight of the heavy batteries. PE consumption has also stayed flat as HDPE gas tanks have already penetrated into the gasoline tank market, displacing steel in developed countries. Electric vehicles may, however, use more PE in the engine parts as the high temperature performance of engineering polymers is not required in electric battery engines.
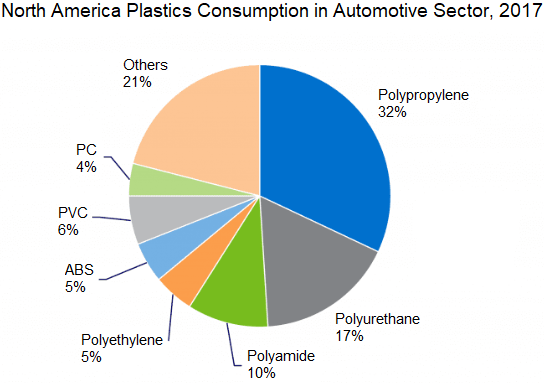
ABS consumption is expected to decline as polystyrene and PP composites with improved properties continue to replace ABS in decorative parts in the interior, which was traditionally dominated by ABS, especially in the United States, due to the material’s gloss. The high price of ABS has also supported the substitution with lower priced polypropylene. In some high-end automobiles, the consumption of ABS will increase for the interior with consumers requiring a higher quality design. However, the overall consumption, particularly in North America and Western Europe, will be counterweighed by a reduction in the size of certain modules, such as the front grill, in turn decreasing the consumption of ABS. The growth in polycarbonate will be driven by the emerging application in car sensors (lenses) in autonomous vehicles, supported by continued electrification and lighting requirements in traditional vehicles.
Implications for Polymer ProducersOverall, the consumption of polymers in the automotive sector is expected to continue to grow. The growth rates will depend on the plastic type, applications in the automobiles, interpolymer substitution, as well as recycling efforts in different regions. The growth rates of plastics such as PP, PA, PC and PE are expected to increase with the introduction of electric vehicles, while the consumption of engineering plastics is expected to slow down.
Author: Ms. Priyanka Khemka, link to the full article.
■
Flame Retardants Increase Product Safety.
Expand articleUsing flame retardant technologies to reduce fire hazards is a basic element of product safety. Flame retardancy is achieved in plastics through chemical reactions that moderate one or more of the elements (fuel, heat, or oxygen) necessary for burning to take place.
There are a number of ambiguous terms used to describe plastics incorporating flame retardant systems, all of which have similar intent: fire retardant, ignition resistant, and self‐extinguishing materials. Even with flame retardant treatment, no plastic can be rendered entirely fire proof. Flame retardant systems are meant to moderate, but not eliminate, eventual combustion.
Flame retardants mitigate fire danger
- Increase plastics ignition resistance
- Reduce the speed of flame spread
- Reduce heat release
- Reduce smoke generation
Elements of successful material selection
- Meet appropriate flammability specification
- Perform in end-use environment with temperature and chemical exposure
- Resin system with appropriate physical properties at a practical cost
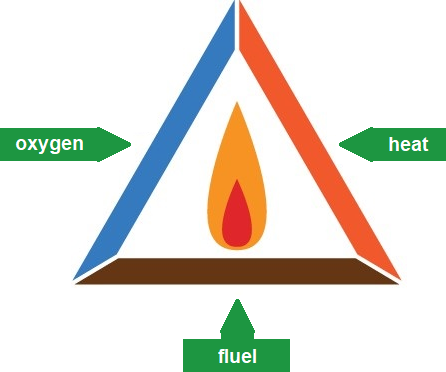
The goal of flame retardant technology is to disrupt one or more of the fire triangle elements necessary for combustion.
Why Flame Retardants?
Flame retardant systems are designed to delay ignition and fire spread as a way to increase escape time.
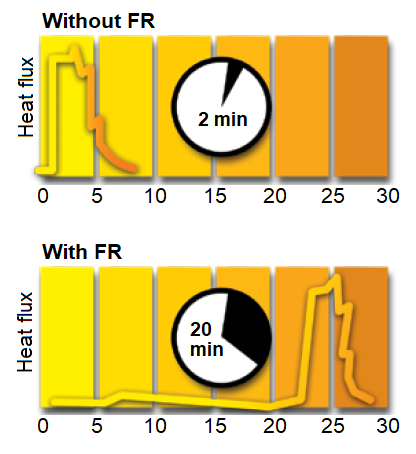
Burning behavior of plastics is not just a material characteristic. Part design and nominal wall thickness are key factors in flammability certification.
How plastics burn
When exposed to heat or flame, thermoplastics undergo pyrolysis, which results in degradation of the resin, releasing gases that become the fuel source for the propagation of combustion.
How flame retardants function
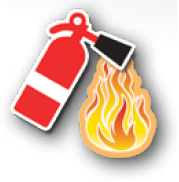
Vapor Phase Inhibition Mechanism
During combustion, flame retardant additives react with the burning polymer in the vapor phase to disrupt the production of free radicals at a molecular level, thereby shutting down the combustion process. This mechanism is commonly used with halogenated flame retardant systems.
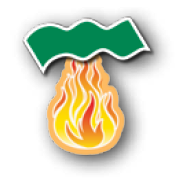
Solid Phase Char-Formation Mechanism
Char-forming flame retardant additives react to form a carbonaceous layer on the material’s surface. This layer insulates the polymer, slowing pyrolysis, and creates a barrier that hinders the release of additional gases that would otherwise fuel combustion. This method is commonly deployed by non-halogen systems using phosphorous and nitrogen chemistries.
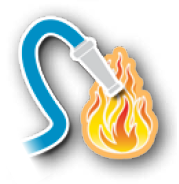
Quench and Cool Mechanism
Hydrated minerals make up a class of halogen-free flame retardant systems commonly used for extruded applications like wire and cable. These systems use an endothermic reaction in the presence of fire to release water molecules that cool the polymer and dilute the combustion process.
![]() |
Vapor Phase Inhibition Mechanism During combustion, flame retardant additives react with the burning polymer in the vapor phase to disrupt the production of free radicals at a molecular level, thereby shutting down the combustion process. This mechanism is commonly used with halogenated flame retardant systems. |
![]() |
Solid Phase Char-Formation Mechanism Char-forming flame retardant additives react to form a carbonaceous layer on the material’s surface. This layer insulates the polymer, slowing pyrolysis, and creates a barrier that hinders the release of additional gases that would otherwise fuel combustion. This method is commonly deployed by non-halogen systems using phosphorous and nitrogen chemistries. |
![]() |
Quench and Cool Mechanism Hydrated minerals make up a class of halogen-free flame retardant systems commonly used for extruded applications like wire and cable. These systems use an endothermic reaction in the presence of fire to release water molecules that cool the polymer and dilute the combustion process. |
Global Standards for Flammability
UL94The UL94 standard, popularized by Underwriters Laboratories (UL) as an element to obtain a UL Listing for end devices, classifies plastics by how different thicknesses of material burn in various orientations.
For example, to achieve the minimum standard UL94 HB, a horizontal specimen less than 3 mm thick must burn at a rate of less than 76 mm/min.
The more typical V-0, V-1, and V-2 classification use samples of varying thicknesses, which is an element of the classification. They require a vertical specimen stop burning within a period rangingfrom 10-30 seconds. The effect of dripped particles is also monitored.
Glow WireIn Europe, the flammability of plastics is often measured using the glow wire test according to IEC 60695‐2‐10 following the Glow Wire Flammability Index (GWFI) or Glow Wire Ignition Temperature (GWIT) methods. To pass glow wire tests, a specimen must either have no flame or glowing for more than 5 seconds while the glow wire is applied for GWIT, or have flame or glowing that extinguish within 30 seconds after removal of the glow wire for GWFI.
Heat, smoke and flame spreadMany other standards can be attributed to factors that are focused on confined space safety and increasing escape time in the event of a fire. The building, transportation, and material handling industries have adopted various test standards that address these concerns, including:
- Aerospace: FAR 25.853
- Mass Transit: ASTM E162/662 (49 CFR 238)
- Building: ASTM E84/1354, UL2043
- Material Handling: UL2335/FM4996
Politem compounds specialized thermoplastics that can reduce heat, smoke and the spread of flames to meet or exceed the ratings required by these industries.
■
Nylon PA6 CARBON FIBER.
Expand articleNylon PA6 CF (Carbon Fiber Reinforced Nylon PA6) is a revolutionary composite material that combines the exceptional properties of carbon fiber with the versatility of nylon. This combination results in a material with superior chemical resistance, low friction and exceptional impact resistance, making it particularly suitable for demanding applications. Carbon fiber, renowned for its extraordinary strength and light weight, gives the material remarkable structural strength, while nylon adds durability and wear resistance.
The light weight of Nylon PA6 CF filament makes it ideal for high-tech industries such as aerospace and automotive, where weight reduction is crucial to improve efficiency and performance. In these areas, the material's impact resistance and stability are essential to ensure the safety and durability of components. Its versatility also makes it suitable for a wide range of other applications, including medical devices and industrial products, where its unique properties can be exploited to improve functionality and efficiency.
Greater Flexibility than PA12 CF: Nylon PA6 CF is distinguished by its superior flexibility compared to PA12 CF. This results in greater elongation at break, making the material more suitable for applications that require not only strength but also some elasticity. This flexibility is especially useful in components that must absorb shock or stress without breaking, such as in some structural parts in aerospace or automotive applications.
Lightness: The combination of nylon and carbon fiber creates a material that is remarkably light. This lightness is critical in industries such as aerospace and automotive, where reducing weight can mean increasing fuel efficiency and improving overall performance. In addition, weight reduction can lead to greater agility and better handling in various engineering contexts.
Excellent Chemical Resistance: Polyamide PA6 CF is known for its excellent resistance to a wide range of chemicals. This makes it ideal for use in aggressive industrial environments, where materials may be exposed to solvents, oils and other chemicals. It is also advantageous in medical device manufacturing, where resistance to sterilizers and other chemicals is essential.
Dimensional Stability: Another significant advantage of PA6 CF is its dimensional stability. Even under stress or heat conditions, the material retains its shape and size. This property is crucial in applications where dimensional accuracy is critical, such as in precision mechanical components or electronic devices.
PROS
- More flexible than PA12 CF
- Higher elongation at break
- Lightness
- Excellent chemical resistance
- Dimensional stability
CONS
- Difficult to paint
- Layers can be visible
Main features
- 3D printing process: FDM
- Tolerance: < 100mm ± 0,60mm; > 100mm ± 0,75%
- Max size: 250 x 250 x 250 mm
- Lead time: < 3 days
Material properties
- Tensile breaking load: 63 MPa
- Modulus of elasticity: 2367 MPa
- Elongation at break: 8%
- Flexural modulus: 5224 MPa
- HDT 0.45 MPa: 179°C
- Izod impact resistance: 12 kJ/m2
Applications of Nylon PA6 CF
Aerospace: In the aerospace industry, Nylon PA6 CF is used for the manufacture of components that combine light weight and high strength. This includes not only structural parts of aircraft, but also internal components such as cladding panels and mounts for on-board electronics. Its resistance to fatigue and high temperatures makes it ideal for the extreme environments typical of this sector.
Automotive: In the automotive industry, polyamide PA6 CF finds application in the production of vehicle parts where weight reduction is crucial to improve fuel efficiency and overall performance. This includes components such as engine mounts, chassis components, interior and exterior panels, and even aerodynamic parts such as spoilers and diffusers.



Medical Devices: In the field of medical devices, Nylon PA6 CF is used to create surgical instruments, diagnostic equipment components and prostheses. Its combination of low friction and chemical resistance ensures that devices are safe, durable and easy to sterilise.
Industrial and Consumer Products: PA6 CF is widely used in a variety of industrial and consumer products, such as sports equipment (e.g. bicycle frames, tennis rackets), hand tools and machinery components. Its strength and durability make it suitable for items that are subjected to regular mechanical stress.
Economical Alternative to Metals: Nylon PA6 CF offers a lightweight yet robust alternative to traditional metals such as aluminium and steel in many engineering applications. This material finds use in areas such as robotics, mechanical engineering and machine building, where weight reduction can improve efficiency and reduce operating costs.
Nylon PA6 CF emerges as a composite material of excellent quality, which stands out for its ability to provide an optimal balance of light weight, strength and high performance, even under demanding environmental conditions. Its versatility makes it extremely suitable for a wide range of industrial and technological applications. From aerospace production, where strength and lightness are paramount, to the automotive industry, which requires materials capable of withstanding mechanical and environmental stresses, PA6 CF establishes itself as an ideal choice.
Despite some limitations, such as difficulties in colouring and layer visibility in 3D printing processes, PA6 CF polyamide continues to be an excellent choice in many areas. These challenges are often overcome through innovation in finishing processes and printing technology, allowing manufacturers to take full advantage of its unique properties.
Furthermore, the increasing focus on more sustainable and high-performance materials is driving the industry towards the adoption of solutions such as PA6 CF filament.Its ability to replace heavier and less environmentally friendly materials, such as certain metals, paves the way for a more sustainable and innovation-driven future.
In summary, Nylon PA6 CF represents a significant step forward in the field of composite materials, offering new possibilities in design and production in a variety of sectors. With its unique combination of lightness, strength and stability, it is well positioned to meet the needs of an evolving market where performance and sustainability go hand in hand.
■